How Parcel TMS Platforms Help 3PLs Control Costs and Manage Margins from Order to Invoice
Third-party logistics providers (3PLs) are integral to the modern supply chain, facilitating efficient transportation and distribution for businesses of all shapes and sizes. But as e-commerce continues to grow and customer expectations around delivery evolve, 3PLs face new challenges in parcel shipping. This article looks at the key obstacles 3PLs are up against and how parcel TMS platforms provide the tools to overcome them.
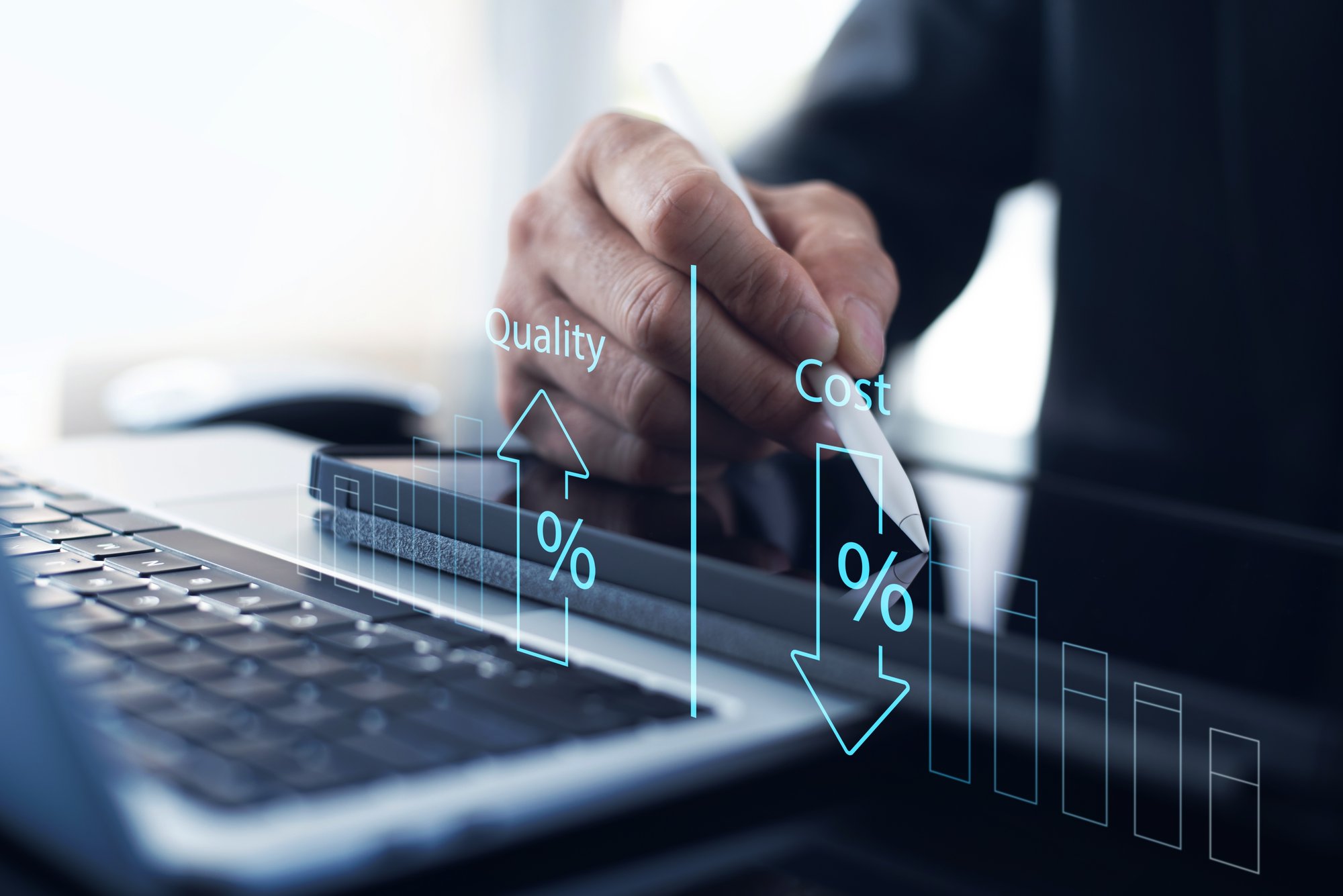
- Parcel Rates Are Rising and Increasingly Complex
Even in the face of lower post-COVID demand, parcel shipping costs have steadily increased in both scope and complexity due to many factors. Carrier base rate increases, fluctuating fuel prices, additional surcharges and accessorial fees, and dynamic carrier incentive discount tiers are making it harder for 3PLs to forecast costs. They face a widening gap between expected costs and the actual costs that appear later in carrier invoices.
As a result, 3PLs face the difficult decision of either absorbing increasing costs (and cutting into their margins) or passing them on to their clients (and risking losing the business). Either option can make it challenging for 3PLs to differentiate their services in an increasingly competitive transportation market.Parcel TMS Optimization Conquers Rating and Service Selection Complexity
For years multi-carrier parcel shipping systems have focused on one task: automating weighing, rating, label printing, and confirming shipments at the end of a warehouse conveyor. Adding cost-effective business rules to these legacy systems to make cost-effective decisions about how, when, and where to use diversified carrier services requires expensive, inflexible, and time-consuming programming.
A new generation parcel transportation management system (TMS) technology has emerged that is designed to address the complexity problem. They provide logistics managers with the controls to simply configure and apply parcel optimization instructions to automate cost-effective decisions during digital storefront, order allocation, fulfillment planning, and shipping processes. Parcel TMS systems enable 3PLs to rank carrier services and calculate accurate shipping costs while avoiding unnecessary spend and unexpected carrier surcharges.
Parcel TMS systems also feature “what if” simulation capabilities. By comparing expected costs at the time of shipping with costs appearing on carrier invoices, 3PL logistic managers can use simulations to test new strategies to eliminate parcel spend leakage and then measure their impact against historical shipping data. “What if I added a new fulfillment node, a new carrier service, different-sized cartons, or a carrier incentive tier?” Actionable insights from simulation scenarios can then be applied using parcel TMS optimization instructions, further improving freight margins. - eCommerce Requires Enterprise-Level Performance
Legacy parcel shipping systems were never designed to support processes upstream from shipping execution. They rely on carrier rating APIs to process shipments, one order at a time. All important decisions about packing, carrier service selection, and billing accounts will have already been made, however poorly, by the time a carton comes to rest at a shipping station scale.
But increasingly, brands are turning to 3PLs for help in determining shipping costs during their customers' digital storefront purchasing process. Consumers want more delivery options based on personalized preferences. This requires iterative processes to calculate multiple rates and times in transit based, potentially, on multiple shipping origins. Carrier APIs are too slow and unreliable (especially during peak when they are most needed) to keep up with performance expectations in eCommerce storefronts. And carriers don’t want their APIs used that way. Some charge accessorial fees for excessive use.
Then once an order is created, there are other shipping-cost-effective decisions that could be made to optimize waves of orders prior to fulfillment. Opportunities for consolidation, mode shifting (parcels to LTL), cost-effective cartonization, and zone skipping are typically lost. Instead, “rules of thumb” and average costs prevail, making margin control very difficult.Parcel TMS Optimization Engines Address the Need for eCommerce Speed
The core of Parcel TMS platforms features an in-platform optimization engine that is designed to calculate rates, estimate times in transit, and apply 3PL instructions at very high speeds. They run independent of carrier APIs and are capable of iteratively processing 20,000 carrier rates per second. This level of performance is suited to the demands of consumers who expect to see many delivery options throughout the online purchasing process.
High parcel TMS performance also opens the door to optimization planning during the order allocation process. 3PL logistics managers can apply instructions against waves of orders and create and compare one or more plans that measure KPIs, including cost per shipment and transit times. The best plans can be released for fulfillment and shipping.
The same parcel TMS optimization process can be applied to historical data to quickly determine simulation results. IT managers have had the advantage of using sandboxes to test technology assumptions. Parcel TMS platforms provide logistics managers with the same benefits. - Intelligent Cartonization is Crucial to Control Shipping Costs
Calculating accurate shipping costs in digital storefronts or during order optimization begins with determining the most shipping-cost-effective way to pack SKUs in an order. If you don’t know what the likely weight and dimensions of cartons will be, it is nearly impossible to accurately calculate carrier rates which makes it difficult to either absorb or pass along costs to the consumer. Unfortunately, rules of thumb and guesswork prevail during these processes.
It’s also a fact that even with parcel shipping costs spiking in recent years, modern warehouse management system platforms ignore shipping costs during pick/pack processes. Their cubing logic has nothing to do with carrier DIM factors or whether it is less expensive to pack in one carton or two. Instead, they solely focus (like legacy shipping systems) on efficiency. If they considered shipping costs, consumers wouldn’t see as many cartons containing small items surrounded by excessive fill.
By ignoring shipping-cost-effective cartonization, 3PLs are often surprised to see unexpected oversize charges and dimensional weight adjustments in their carrier invoices. These fees can have a dramatic impact on shipping costs and freight margins.Parcel TMS Cartonization Instructions Help Control Cost-Effective Packing
Parcel TMS solutions use cartonization algorithms to determine the best way to pack an order based on SKU-level instructions. These can include fragility, don’t pack with (ex. hazmat), don’t stack, rolling and nesting, and other rules that take the weight, dimensions, and shape of SKUs into account.
Together with instructions about carrier DIM factors and available carton sizes, parcel TMS systems can better predict shipping costs in digital storefronts and order allocation while enforcing better packing methods in WMS fulfillment processes. They can also help avoid costs associated with returns by reducing damage caused by poorly packed cartons. - Making and Keeping Delivery Promises
Today's consumers have high expectations for shipping. According to McKinsey research presented at the Parcel Forum 2024, consumers still demand fast, reliable, and cost-effective delivery options, often expecting same-day or next-day service. However, delivery predictability is increasingly important as well, which requires a high level of analysis and planning. Meeting these demands presents a significant challenge for 3PLs, who must find ways to offer quick turnaround times without sacrificing quality.
But the pressure to meet consumer expectations can put a substantial strain on operations. If 3PLs cannot keep their delivery promises, they risk losing customers and damaging their reputation. Additionally, the cost associated with expedited shipping options can further complicate the already tight profit margins that many 3PLs operate under.
Unfortunately, legacy shipping systems are willing to believe what carrier APIs tell them about expected time of delivery. These predictions are not always accurate. They are often inconsistent with a carrier’s past delivery performance under similar conditions.Parcel TMS Leverage Machine Learning to Make Better Delivery Predictions
Modern parcel TMS platforms consider but do not rely on carrier APIs to determine times in transit. Instead, they use machine learning to evaluate a carrier’s performance based on delivery area (zip, city, state, etc.), as well as the day of the week, week of the month, and month of the year.
In addition, delivery promises made during order creation often change based on circumstances during order allocation, fulfillment, shipping or as the shipment works its way through the carrier network. Parcel TMS platforms monitor those circumstances and can change routing decisions dynamically or proactively notify the 3PL of delivery exceptions. - Scalability, Security, and Cost of Technology Ownership Issues
Systems that were designed to perform a specific function don’t react well when they are recruited to perform a different function. The same is true for legacy shipping systems, which a Gartner analyst once referred to as a glorified typewriter, printing out carrier labels on demand.
As described above, the challenges facing 3PLs require a breadth of capabilities, performance characteristics, and flexibility that are quite beyond the remit of parcel shipping systems. Many were designed for on-premise deployment but have been redeployed in hosted cloud environments. Manual intervention is required to scale server instances under load. Their security models do not anticipate the modern concerns about redundancy, personal privacy, and data protection.Parcel TMS Platforms Take Advantage of Modern Architectures
Next-generation parcel TMS platforms were designed from the ground up to take advantage of cloud-native, microservice based architectures. They auto-scale underload to optimize availability. They are highly redundant and can more easily failover to other regions. Most are SOC II, type 2 certified. But more importantly, they were designed to shift control of business rules from IT personnel and programming engineers to logistics business users. 3PLs costs of ownership are lower because changes to optimization instructions can be made in minutes instead of weeks and then change as business conditions change.
Managing Parcel Cost Control Complexity with Sendflex Parcel TMS
The challenges 3PLs face in parcel shipping are multifaceted and complex. From rising shipping costs and operational performance to increasing consumer expectations and margin management, the modern logistics environment demands more agile, performant, and innovative technologies. Sendflex emerges as a powerful parcel TMS resource for 3PLs, offering a comprehensive platform that addresses these challenges head-on.
LEARN
Download
The Five Parcel TMS
Value Pillars
EBOOK
Learn why controlling costs, capacity, carbon, and customer experiences matters in the B2C delivery economy
Shippers who are used to relying on a primary parcel carrier with unlimited capacity must now manage a broader portfolio of carriers, all with different capabilities, performance records, constraints, and rate structures.
DELIVERY CONSULTATION
See What Sendflex Can Do for You
Are you struggling to keep up with the consumer demand for faster, cheaper delivery service options? Is it time for a smart multi-carrier parcel solution?
Whether deployed on premise or accessed from the cloud, our shipping platform apps and APIs support your entire extended enterprise: carrier selection, rating and routing, cartonization, shipping and drop shipping, tracking, and returns.
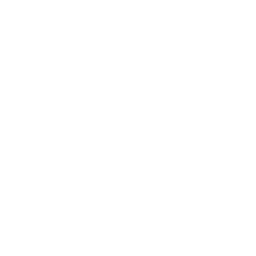