Article: How to Plug Spend Leakage with Intelligent Parcel Management Systems
The problem with parcel spend leakage is not only that it adds unexpected expenses which erode margins but also that it is largely avoidable, and shippers that are not addressing this challenge are losing out on the potential for significant savings.
Spend leakage happens when there are no systems monitoring parcel-related shipping decisions to ensure ever-increasing carrier surcharges are anticipated and avoided. The problem has become more critical in an increasingly complex eCommerce landscape, where shippers have diversified their carrier network and implemented decentralized, omni-channel fulfillment strategies to deliver on time from inventory locations closer to their customers.
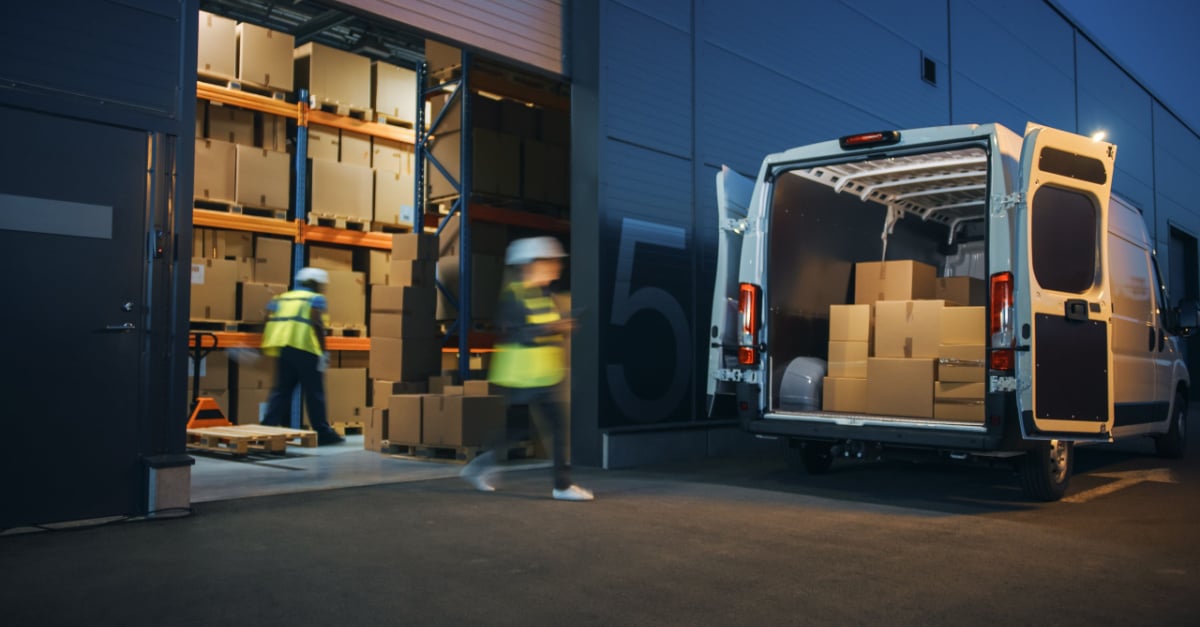
To help address their multi-carrier shipping management challenges, shippers are increasingly reliant on technology to streamline decision-making processes. However, legacy shipping systems were never designed for this purpose. They were designed to automate shipping (usually for a primary carrier like UPS, FedEx, or USPS) at the end of a warehouse conveyor when the opportunity to save money by considering other multi-carrier shipping services or packing methods has passed. Hard coding basic business rules into these legacy systems comes at the cost of custom programming by scant IT resources, long project timelines, and inflexibility.
That is why more shippers are turning to the next generation of parcel shipping systems that add configurable rules to simplify complex decision-making not only in shipping but in upstream quoting, planning, and fulfillment processes.
What is Intelligent Multi-Carrier Shipping Software?
Intelligent multi-carrier parcel management offers logistics managers the controls they need to monitor and optimize costs, available capacity, and customer delivery experiences. These systems provide powerful capabilities that help simplify complexities posed by modern B2C fulfillment environments:
- No-code, configurable business rules – Intelligent parcel management systems provide wizards and drop-downs to define business rules, making it easy for logistics managers to apply automated parcel decisions in order entry, fulfillment, and shipping, and then change rules as necessary. Logistics managers can accomplish in minutes what would take programmers weeks to code and test.
- High-speed rating and routing engines – By removing the reliance on slow and unreliable carrier APIs, shippers can process thousands of carrier rates per second, enhancing the consumer’s online checkout experience and optimizing planning processes upstream from shipping.
- Cartonization algorithms – Optimized cartonization allows shippers to save on shipping costs by applying rules for packing orders in a way that eliminates shipping “air” while improving cube utilization and sustainability by using less corrugated material.
- Parcel optimization planning – Advanced optimization business rules automatically determine how, when and where to use diversified carrier services based on many factors, including cost, shipment attributes, carrier performance, customer preferences, and more.
- “What if” simulations – Logistics managers can apply configurable business rules to historical data and run “what if” simulations to measure the impact different assumptions and constraints (such as carrier alternatives, fulfillment centers, and carton sizes) will have on cost and delivery performance.
Intelligent parcel shipping systems can automate multi-carrier shipping execution, or they can simply add a layer of intelligence to legacy shipping systems to help with upstream decision-making — as in shopping carts, order fulfillment, and packing.
12 Areas Where Intelligent Parcel Management Systems can Reduce Parcel Spend Leakage
More importantly, intelligent parcel management systems can reduce unexpected costs by helping to monitor and automate decisions that prevent spend leakage and margin erosion. Below are 12 spend leakage opportunities that intelligent parcel shipping systems target:
Address Correction Surcharges
Address correction surcharges are still very common and often go unnoticed on carrier invoices. They are not insignificant. For example, UPS charges $19.50 for each address correction. Making matters worse, some shippers pay recurring address corrections for the same address. These fees can bloat a carrier invoice very quickly. UPS and FedEx provide address validation APIs. Intelligent parcel shipping systems use a carrier’s own address validation format as a “source of truth” to ensure the address that a carrier believes is correct is printed on the label, thereby avoiding unexpected surcharges and disputes. These validated addresses are then applied in order entry or in shipping.
Residential Surcharges
Residential surcharges are extra fees levied for deliveries to residences as opposed to commercial locations. Like address correction fees, residential surcharges are not trivial. UPS charges $5.25 extra for ground deliveries. They are often unavoidable for B2C shipments, but they at least should be anticipated for shippers to understand the true landed cost of a delivery as a residential surcharge could wipe out profitability on a sale.
It is not uncommon for carriers to make mistakes in classifying what constitutes a residence versus a commercial location because they use USPS Residential Delivery Indicator (RDI) data or their own subjective criteria to make that determination. RDI and driver curbside observations are not always accurate. The result? Shippers pay residential surcharges for commercial deliveries.
Next-generation shipping systems use location intelligence to determine whether a location is actually a residence or not. If it is a residence, what kind of residence? Validating addresses in this way helps shippers plan ahead and budget for the added cost of deliverying to a residence or to dispute incorrectly classified residential surcharges.
Reduced Costs Using Regional Carriers
Regional carriers offer local delivery services that can help companies reduce their parcel shipping costs. But shippers need to weigh different factors involved in identifying and deciding when, where, and how regional carriers should be used..
Intelligent parcel shipping systems enable logistics managers to define optimization instructions that qualify the use of regional carriers based on weight, ZIP codes serviced, and other performance criteria such as on-time delivery, billing errors, and damage. Instructions can also consider routing to regional carriers without risking the loss of primary carrier contract incentives (see below).
Premium Service Downgrades
With shipping costs on the rise, shippers need to control the use of premium carrier services when ground services can achieve the same result. Intelligent routing rules can enforce cost-effective carrier service selections and downgrade carrier service selections that were improperly made. This is where embedding intelligence routing decision controls throughout the fulfillment process can pay big dividends without compromising delivery promises.
Pickup Limit Surcharges
During holiday peak periods, carriers will often impose limits on the number of shipments they will pick up in a day. If a shipper exceeds the pickup limit, some carriers will levy pickup limit surcharges. Intelligent parcel shipping systems monitor shipment volumes for each carrier in real-time and apply carrier contract compliance rules to route to an alternate carrier service once the pickup limit has been reached, thereby avoiding unexpected pickup surcharges on their next carrier invoice.
Loss of Carrier Contract Tier Incentives
When a shipper has tier incentives in their primary carrier contracts — discounts that are given to customers that meet certain targets in terms of parcel shipment spend, usually calculated as 52-week rolling averages — they want to do everything they can to avoid losing these incentives. Failure to do so can result in substantial and unexpected shipping costs.
In the same way that intelligent parcel shipping systems monitor daily pickup volumes and make carrier routing decisions to avoid surcharges, incentive target run rates are monitored to ensure no other carrier’s services are selected until the incentive tier has been met, even if another carrier would be less expensive in the short-term.
Dimensional Weight Adjustments
Carriers’ profitability depends on their ability to maximize the cubic space utilization of their vehicles. Their goal is to haul more weight in less space. This is why when shippers pack boxes in a way that wastes space, carriers calculate shipping charges based on dimensional (DIM) weight instead of actual weight to make up for the incremental capacity and revenue loss.
To prevent these rate adjustments, intelligent parcel shipping systems use cartonization algorithms to determine the most transportation-cost-effective way to pack orders, applying rules to minimize wasted space. Automated rules take carton sizes and SKU dimensions, weights, and shapes into account, as well as carrier DIM factors and shipping unit minimums. Or routing rules will select an alternative carrier with a less expensive DIM factor.
Corrugated Waste
Everyone has had the experience of receiving a shipment where a tiny item is packed in a large carton filled with fill material. Not only is this environmentally unfriendly and costly in terms of DIM fees, but also wasteful in terms of corrugated material which has seen high price increases in recent years.
An intelligent parcel management system helps reduce spending on corrugated material in two ways. First by using cartonization algorithms to select the smallest carton necessary to pack an order. But also to run data-driven simulations against shipping history to determine the right combination of box sizes on hand to cost-effectively fulfill orders in the future. Having the right set of carton sizes can save shippers over 5% in transportation costs.
Damage Returns
Nothing ruins a customer’s delivery experience more than receiving a damaged product. Not only is it wasteful in terms of shipping expense and lost revenue but also the cost of processing the return shipment. In the same way cartonization instructions can minimize DIM weight adjustments and corrugated waste, they can also help avoid returns due to damage caused by improperly packed SKUs.
Intelligent parcel shipping systems can determine how to optimally pack cartons, using fragility rules to recommend fill and padding requirements, as well as an orientation within the carton. This can ensure that the items in the shipment are cushioned and secure, reducing the chance of damage. In that way, shippers can reduce their total number of returns by minimizing damage to their products and their brand.
Carrier Performance Instructions
Shippers sometimes only consider shipping rate fees as their basis for using a carrier service. But there are other costs that should be taken into account, such as those incurred as a result of performance lapses. Time and out-of-pocket expenses related to missed deliveries, damaged shipments, billing mistakes, and customer complaints add up. While it may be tempting to prioritize “rate shopping” when making a carrier service decision, a more objective, data-driven approach may help, when the rate savings may not be worth the risk of compromising the delivery service and adding indirect expenses that affect the bottom line.
For example, a carrier may charge $10 for delivery to a particular ZIP code location. But if historical data reveals that the added cost of missed deliveries, damage returns, and billing errors during that period averaged 75 cents a parcel, then the actual cost to compare should be $10.75. Intelligent parcel shipping systems can apply these value coefficients to routing decisions, promoting or demoting carrier services in rank. Having the ability to objectively rank carriers in that way takes subjectivity out of decision-making.
Consolidated Zone-Skipping
Zone-skipping is the strategy of aggregating and shipping multiple parcel shipments directly to locations in a zone, bypassing intermediate zones, hubs, and sort centers. This strategy enables shippers to save costs and reduce delivery times while lowering damage claims.
Because most legacy shipping systems are deployed in the last 100 feet of a warehouse and only process one order at a time, they lack the visibility to identify zone-skipping opportunities further upstream. Intelligent parcel shipping systems can evaluate groups or waves of orders and apply instructions to automate zone-skipping decision-making processes.
Parcel Cost Variance
The proliferation of surcharges and other fees levied by parcel carriers has grown steadily over the years. The added complexity of calculating accurate rates has created an increasing gap between what a shipper expects to pay and the charges that show up on a carrier invoice. The gap is caused by unexpected surcharges that either could have been avoided by better decision-making in order entry, fulfillment, or shipping processes, or by carriers incorrectly billing for shipping services that did not occur.
An intelligent parcel management system is designed to monitor and prevent unexpected surcharges but also share manifest data with freight auditors to compare the manifest against carrier invoices, thereby measuring parcel cost variances. By closing the loop in this way, logistics managers can identify areas where better decision-making can lead to continuous improvements to reductions in spend leakage.
Eliminate Spend Leakage with Intelligent Parcel Management
Adding an intelligent layer to parcel management can reduce total spending by avoiding unexpected surcharges, eliminating waste, keeping track of progress toward targets, reducing damage, identifying lower-cost shipping options including consolidation and zone-skipping strategies, and correcting billing errors.
Sendflex helps shippers save money by providing them with the controls they need to manage parcel shipping costs, capacity utilization, and customer delivery experiences. This next-gen shipping system lets shippers expand their carrier network and automate cost-effective shipping decisions with no-code, configurable optimization instructions that can be applied to shopping carts, order entry, fulfillment, and shipping. Sendflex is the perfect platform for today’s dynamic B2C eCommerce delivery environment.
To learn more about Sendflex, request a consultation with us today.
LEARN
Download
The Five Parcel TMS
Value Pillars
EBOOK
Learn why controlling costs, capacity, carbon, and customer experiences matters in the B2C delivery economy
Shippers who are used to relying on a primary parcel carrier with unlimited capacity must now manage a broader portfolio of carriers, all with different capabilities, performance records, constraints, and rate structures.