Parcel Simulators: Proving Intelligent Cartonization ROI
In the dynamic and complex world of supply chain logistics, staying one step ahead of the competition is a constant challenge, and logistics managers are under constant pressure to implement innovative fulfillment strategies. But trial and error can be very costly, disruptive, and potentially tarnish the brand's reputation. That’s why logistics managers are turning to more intelligent parcel technologies with simulation capabilities that allow operational ideas to be tested in virtual environments, significantly minimizing cost and disruption risks.
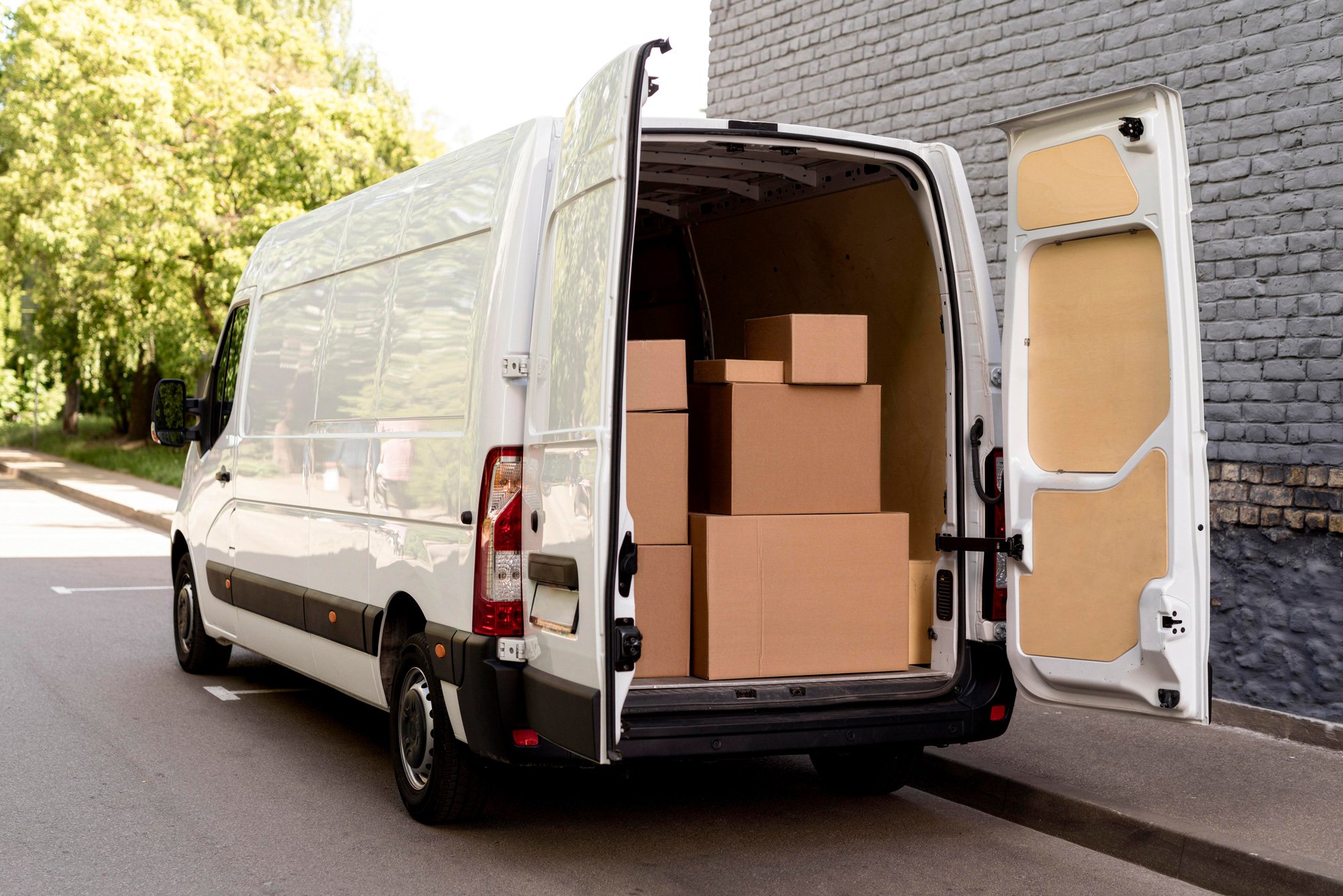
The spotlight currently falls on packing optimization, an essential logistics component for the modern eCommerce dominated market. Shockingly, parcel shipments in certain product categories contain up to 64% air. Considering the average American receives 61 packages annually, the magnitude of wasted space, environmental impact, and shipping cost is staggering.
This article dissects the implications of ineffective packing decisions - from inflated shipping costs and excess corrugated waste to increased damages and returns. It will further explore how parcel simulators can calculate the cost benefit of optimized packing, thereby creating a more sustainable and efficient logistics process.
Poor Packing Decisions Inflate Carrier Invoices
Parcel carriers make money the same way hotels do. They carefully manage space and time.
Hotels | Parcel Carriers | |
Space | Room Occupancy | Cube Utilization |
Time | Nights Stayed | Days in Transit |
In reality though, parcel carrier rates have historically been largely determined by weight, zone, and service level, like ground vs. express. This is despite the fact that, as one parcel executive aptly put it: "the truck weighs more than the parcel load." In other words, the entire parcel network transports an astonishing amount of empty, unused space. With the surge in parcel volumes driven by B2C eCommerce, carriers have increasingly emphasized shipment dimensions as a critical pricing factor.
As a result, shippers, who previously hadn't linked inefficient packing practices to shipping costs, started noticing unexpected dimensional weight adjustment fees on their carrier invoices. These adjustments, which often inflated shipping costs by over 10%, were the carrier's not-so-subtle way of saying, “Stop shipping air!"
While this pricing paradigm has been in place for several years now, most shippers still lack the necessary controls to determine whether it is more shipping-cost-effective to pack orders in one carton or multiple cartons. Balancing minimum charges against volume factors can vary based on the carrier, their service level, and dim factor, as well as the ship from and ship to locations. Additionally, traditional warehouse management systems' (WMS) cubing algorithms universally focus on optimizing labor costs, which decrease with the addition of automation, while neglecting to factor in transportation costs, which are constantly on the rise.
Poor Packing Decisions Increase Wasted Corrugate, Damages, and Returns
The surge in eCommerce has triggered several supply chain transformations, including smaller, more frequent corrugated carton shipments. This increased demand for cartons has driven corrugated costs higher. Consequently, shippers not only face unexpected dimensional weight adjustments but also incur excessive corrugate expenses when small items are packed in oversized cartons - a scenario all too familiar to most consumers. The costs of fill needed to occupy the wasted space in large cartons further add to this financial burden.
Uncontrolled packing processes can also lead to damaged goods. Decisions about corrugated cardboard grade selection, SKU orientation within cartons, and the amount of fill used can directly influence the likelihood of damage during transit. Worse, damage inevitably leads to returns, triggering a domino effect of consequences.
- Negative customer experience: Damages and consequential returns processes create an unsatisfactory experience that can severely harm loyalty and repeat customer metrics.
- Sustainability concerns: Excessive corrugate and fill are not only expensive, they also reflect poorly on a shipper’s commitment to environmental responsibility and sustainability, further tarnishing their reputation among customers.
- Increased costs: More corrugate and fill, replacement products, and added shipping costs for returns and replacements significantly inflate fulfillment costs, eroding margins and eating into profits.
The implications of poor packing extend beyond mere shipping inefficiencies. Recognizing the interconnectedness of these issues is the first step towards implementing smarter, more sustainable, and cost-effective packing strategies.
Optimizing Packing Decisions with Parcel Simulation Technology
Given the direct and indirect costs linked to inefficient packing processes, it's obvious that smarter decisions need to be made during the fulfillment process. However, these decisions are complex due to the myriad factors that need to be carefully weighed - all while warehouse personnel are under pressure to get shipments out the door as fast as possible to meet delivery promises. Making these complex decisions quickly is beyond the realm of human intelligence alone.
Enter the new generation of AI-driven parcel orchestration platforms. These platforms offer planning and simulation capabilities upstream from traditional parcel execution systems. They start by quantifying the problem in terms of potential shipping cost savings, particularly those tied to packing practices.
“Parcel simulators apply packing business rules, carrier rates and dim factors, and cartonization algorithms to historical shipping data and instantly determine the best way to pack SKUs based on their weight, dimensions and shapes, as available carton sizes”, said Chris Brejak, Sendflex CRO. “You can compare the costs of what happened against what should have happened, and then apply those insights to order fulfillment processes.”
Parcel simulators provide logistics managers with the ability to test “what if” scenarios in a virtual environment to answer complex packing questions like:
- What if I use a carrier with a different dim factor?
- What if I change my percent fill?
- What if I change the orientation of how a SKU is packed?
- What if I add a different size carton to the mix?
Testing different assumptions can yield significant cost saving results – on average 16% – all without the need for costly real-world trial and error tests. The results of iterative simulations can then be applied to parcel orchestration planning processes for ultimate optimization.
Optimizing Carton Size Mix with Cartonization Simulations
The decision about which carton to use during the packing process can easily be automated with parcel orchestration solutions. However, a more strategic challenge logistics managers face is determining the optimal mix of carton sizes. While having hundreds of carton sizes on hand would be ideal from a transportation cost perspective, inventory carrying costs make this impractical. Conversely, having too few can lead to the cost overruns described above. Even new box-on-demand hardware requires an intelligence layer to guide them towards the right goal.
Fortunately, cartonization algorithms can automate these decisions, using simulations to run through millions of iterations and find the most optimal mix of carton sizes.
James Malley, Paccurate CEO, explains, “Our PacSimulate process eliminates the guesswork from carton inventory decisions. It uses cartonization algorithms to balance efficiency, shipping costs, and corrugate costs. This allows you to determine the perfect set of cartons with unprecedented accuracy."
Sendflex and Paccurate: Revolutionizing Operations through Parcel Simulators and Intelligent Cartonization
The integration of parcel simulators with intelligent cartonization technology is yielding significant benefits, not only in terms of reducing shipping costs but also minimizing waste and carbon footprint. This innovative approach harnesses the power of artificial intelligence, enabling businesses to make smarter, more efficient packing decisions that have a far-reaching positive impact.
Sendflex and Paccurate offer comprehensive solutions that revolutionize logistics processes. Start exploring the possibilities by visiting Sendflex and Paccurate today.
LEARN
Download
The Five Parcel TMS
Value Pillars
EBOOK
Learn why controlling costs, capacity, carbon, and customer experiences matters in the B2C delivery economy
Shippers who are used to relying on a primary parcel carrier with unlimited capacity must now manage a broader portfolio of carriers, all with different capabilities, performance records, constraints, and rate structures.