Stuck in a Custom Programming Ditch? No-Code Parcel TMS Puts Logistics Managers Back in the Driver's Seat
Sendflex parcel TMS frees shippers from the constraints of hard-coded legacy shipping systems, unlocking new levels of flexibility, agility, and intelligent insights.
In the ever-evolving landscape of eCommerce, decisions about how to cost-effectively pack, select from a growing diversity of final mile carrier delivery options, and efficiently execute shipments have become increasingly complex. Legacy shipping systems lack the ability to embed business rules without costly custom programming and long project timelines.
As illustrated in this article’s 10 FAQs, Sendflex parcel TMS offers a no-code approach to data-driven, cost-effective decisions.
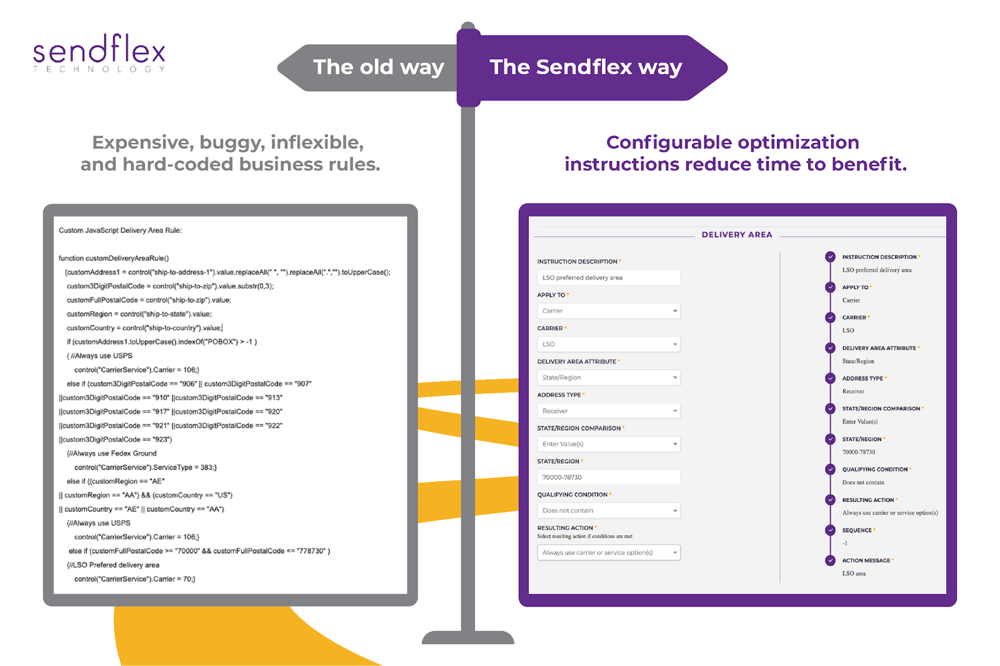
Complexity Is Confounding Legacy Parcel Shipping Systems
Amazon has revolutionized eCommerce fulfillment, emphasizing faster, more cost-effective and sustainable deliveries from fulfillment centers located closer to end-consumers. This strategy has not only transformed the industry but also escalated consumer expectations for more delivery options. Research indicates that 90% of consumers expect standard two- or three-day shipping, with 32% willing to abandon their carts if quoted shipping times are too long.
In response, traditional brick and mortar retailers are playing catchup, implementing decentralized omni-channel fulfillment models while diversifying their last-mile small package delivery networks. Gone are the simpler days of relying on a single carrier to deliver from a centralized distribution center. Today, many more factors go into how, when, and where to pack and ship orders for timely delivery. And with eCommerce currently accounting for only 16% of retail sales, both the potential for growth and the increased shipping management complexity introduced by these strategic shifts are profound.
Unfortunately, most digital storefronts, OMS, WMS, TMS, and shipping systems were never designed to handle the complexity that has crept into the parcel industry. They were designed to maximize fulfillment efficiency when shipping cost control amounted to simple “rate shopping” and applying tribal knowledge and rules of thumb. As a result, according to Intelligent Audit’s CEO Hannah Testani, today there is often a 20% gap between what shippers expect to pay for shipping and the actual costs that show up on carrier invoices which include a growing array of unexpected surcharges and fees.
Of course, some legacy shipping system vendors can customize programs, using hard coded scripts to apply simple shipper-specific business rules during the shipping execution and labeling process. But these modifications are costly and involve long project timelines which tax scarce IT resources. The results are often buggy, brittle, and not very well maintain or supported. Moreover, applying these business rules downstream from digital storefront quoting, order allocation, and warehouse fulfillment is usually too late in the process to have any real cost and delivery quality impact. Logistics managers are thus left unable to adapt to ever-changing eCommerce logistics challenges.
Today's shippers need a way to embed automated decision-making at every fulfillment stage to effectively control shipping costs, sustainability, and delivery quality. Sendflex has stepped up to meet that demand with a parcel TMS platform that empowers logistics managers with the ability to easily configure complex instructions to optimize intelligent packing, routing, and shipping decisions.
Sendflex Parcel TMS Conquers Complexity
Sendflex’s Parcel TMS platform follows the path forged by traditional freight TMS systems, which always had deal with a more complex and fragmented ground, rail, and ocean transportation industry. Like freight TMS systems Sendflex grants non-technical logistics managers the autonomy to configure instructions related to routing, rating, routing, load planning, and tracking processes across hundreds of carriers.
But unlike freight TMS systems which are more back-office oriented, Sendflex’s onboard optimization engine performs at the speed of eCommerce, efficiently processing over 20,000 rates, times in transit, cartonization, and instructions per second. Sendflex is perfectly at home operating alongside high-speed fulfillment systems, monitoring orders, carrier constraints, and supporting real time intelligent decisions across the enterprise.
Best of all, unlike legacy parcel systems that can only look at one order or shipment at a time, Sendflex can look across batch waves of orders and apply optimization instructions to maximize savings. Sendflex can also run “what if” simulations that enable logistics managers to gain insights and measure the impact of strategic decision-making before operationalizing those instructions during execution processes.
10 FAQs About How Sendflex Parcel TMS Optimizes Complex Decision-Making
Below are ten frequently asked questions about how Sendflex parcel TMS can be used to reduce costs and improve performance without having to pay for custom programming.
- How do I diversify my carrier network without risking loss of my primary carrier tier incentives?
For the foreseeable future, shippers will need to rely on major parcel carriers (UPS, FedEx, USPS, and now Amazon) to deliver the bulk of their parcel volumes even as they start to expand their network to include 3PLs, regional carriers and local couriers. Shippers work hard to negotiate the best primary carrier contract they can, which includes valuable tier incentives. If they don’t achieve those primary carrier incentives, it could offset any savings they hoped to realize by leveraging alternative carrier delivery services. Or worse.
Sendflex solves that problem by monitoring spending levels for all carriers and automating data-driven multi-carrier routing decisions. Logistics managers can configure an instruction that enables routing to an alternative carrier service but only when they are on track to achieve their primary carrier’s tiered incentive targets. This ensures compliance with primary carrier contract commitments, preserving discount levels while enabling other delivery service alternatives. - How do I reduce use of expensive express services by more accurately predicting carrier delivery times?
The pressure is on eCommerce shippers to make and keep delivery promises. But so long as free shipping is the norm, care must be taken to accurately determine shipping costs to ensure margins are preserved or at least understood. Why use express services when a ground service is likely to get it there in time?
Sendflex’s optimization engine calculates rates and times in transit based on actual delivery performance to specific destinations instead of relying on published ETAs. This can mean automatically shifting to a ground service when a package will likely be delivered at the same time as an express service.
Sendflex also monitors carrier cutoff times. This ensures that if a shipment designated for ground delivery cannot make the daily carrier pickup, it will be either rerouted to a carrier that can or is rerouted to an express service for the next day’s pickup.
Zone skipping services such as Maergo are also supported by Sendflex. This means that shippers can using Sendflex planning processes to take advantage of 2 day delivery to zones 5+ at ground rates instead of incurring express service costs for the same delivery result.
- How do I reduce unexpected dimensional weight adjustments and oversize charges on my carrier invoices?
We’ve all had the experience of receiving large cartons with tiny products surrounded by fill. And no one likes it. It makes for a horrible sustainability experience for consumers as they have more waste to haul off to a landfill. Shippers incur the cost of using excess corrugated and fill material. And carriers are unable to maximize cube utilization in their vehicles, resulting in lost revenue which they aim to recover in the form of dimensional weight adjustments.
The culprit is uncontrolled packing. Most, if not all, OMS and WMS systems do not take transportation costs into account when designating pick/pack instructions. Instead, they focus on efficiency because they lack the business rules necessary to reduce shipping costs. Sendflex can enhance WMS packing decision with cartonization instructions that take a wider range of factors into consideration, including:- Carrier DIM factors
- Carrier shipping costs, and minimums (1 carton or 2?)
- Available carton sizes
- % fill, thickness
- Customer preference
- SKU attributes: fragility, hazardous, shape, orientation
- Packing rules: don’t pack with, pack with, nesting, rolling, bagging, stacking
Submit an order or batch of orders to Sendflex’s API and within milliseconds Sendflex will apply cartonization instructions and return the most transportation cost-effective way to pack.
In addition to monitoring dimensional weight adjustments, Sendflex instructions can be set up to monitor shipping processes and avoid situations that are likely to result in parcel carrier surcharges which have proliferated in recent years. For example, instructions can be set up to limit the use of certain carrier services such as SmartPost and Mail Innovations where oversize surcharges are applied when weights exceed contractual limits. - How do I determine what the optimize set of carton sizes should be?
One aspect of the unexpected dimensional weight adjustment problem is that shippers don’t know which size cartons to keep on hand. An infinite number of sizes would be ideal, but not very practical in terms of inventory carrying costs. Having too few cartons will likely result in more dimensional weight adjustments.
Sendflex can use the PacSimulate tool to determine the most cost-effective combination of carton sizes to keep on hand. Sendflex can then run what-if simulations to determine what the actual transportation and material cost savings will be. - How do I reduce damage incidents and the cost of returns?
Another aspect of operationalizing cartonization controls is ensuring packing instructions include factors that will eliminate, or at least reduce, product damage and returns. As mentioned above, Sendflex cartonization instructions can include SKU specific attributes such as fragility, % fill, don’t stack, and padding. Sendflex returns animated diagrams that specify damage-avoidance packing procedures.
Sendflex also enables logistics managers to apply a value coefficient that will impact carrier service selection ranking based on performance factors such as damage. A carrier’s shipping charge to a specific destination may be $15.00, but it could be adjusted to $18.50 based on their likelihood to cause damage, thereby demoting the carrier in rank, taking into account the true cost of using that service.
Logistics managers can also use instructions to disqualify use of certain carrier services based on very granular variables such as destination zip codes or cities, SKU attributes, shipment attributes, and insured values. - How do I manage more granular shipping and handling charge markups?
For those shippers that can pass along shipping costs to their customers, there is usually a need to adjust actual shipping costs based on customer status, shipment value, destination zone, and a variety of other factors.
Sendflex instructions can apply these calculations during digital storefront quotation processes or fulfillment, accurately updating customer service, billing, and other enterprise systems. - How do I ensure I comply with customer shipping preferences?
It is common for customers, especially large customers, to specify how they want their orders packed, which carrier services to use, or how they want to be billed. Failure to do so can result in penalties or lost brand value.
Logistics managers can easily define and apply customer preference instructions to orders at any point in the fulfillment process. Sendflex simulator can quantify what the impact of customer-specific instructions would have been had they been applied to a customer’s shipping history. - How do I ensure I don’t exceed pickup limits imposed by carriers during peak periods?
It is now common during peak shipping periods for carriers to limit pickup volumes from specific locations. Exceed that volume can result in carrier surcharges or delivery disruptions.
Sendflex can be set up to monitor daily shipment volumes and then automatically reroute to alternative carrier services once the primary carrier pickup limit is reached. A more granular “smart cap” instruction can be set up to limit pickups for certain carrier lanes while enabling pickups for those lanes where a carrier has more capacity. In this in other ways, Sendflex aligns shipper optimization with carrier network optimization. - How do I know what the actual impact of a General Rate Increase will be?
Every year the major parcel carriers announce a rate increase and every year every shipper knows that the actual increase will be higher than the published increase based on a shipper’s own shipping profile. Analyzing the actual impact can often mean having to engage expensive consulting services.
Using Sendflex’s simulator, shippers can rerun historical shipping data using the new rates and surcharges and model what the impact would be had the GRI been in place. This enables shippers to proactively look for ways to use instructions to reduce the impact of the price increase. - How can I use Sendflex parcel TMS optimization intelligence to enhance my existing systems?
Many shippers have been months and sometimes years ensuring their enterprise systems, including legacy systems, work just the way they want them to work. Ripping and replacing systems is sometimes a painful process.
Sendflex can be used to enhance any ERP, OMS, Freight TMS, WMS and legacy shipping system. We make it easy for our APIs to be used to automate cartonization, routing, rating, shipping, tracking and return processes.
Revolutionizing Parcel Management with Sendflex Parcel TMS
Sendflex parcel TMS platform transforms the way shippers manage complex route optimization. This groundbreaking system empowers users with complete control, allowing the configuration of intricate instructions in mere minutes–a process that would otherwise take weeks of custom programming, testing, and deployment.
For a seamless transition to agile eCommerce fulfillment, contact Sendflex today.
LEARN
Download
The Five Parcel TMS
Value Pillars
EBOOK
Learn why controlling costs, capacity, carbon, and customer experiences matters in the B2C delivery economy
Shippers who are used to relying on a primary parcel carrier with unlimited capacity must now manage a broader portfolio of carriers, all with different capabilities, performance records, constraints, and rate structures.
DELIVERY CONSULTATION
See What Sendflex Can Do for You
Are you struggling to keep up with the consumer demand for faster, cheaper delivery service options? Is it time for a smart multi-carrier parcel solution?
Whether deployed on premise or accessed from the cloud, our shipping platform apps and APIs support your entire extended enterprise: carrier selection, rating and routing, cartonization, shipping and drop shipping, tracking, and returns.
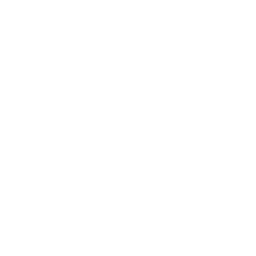